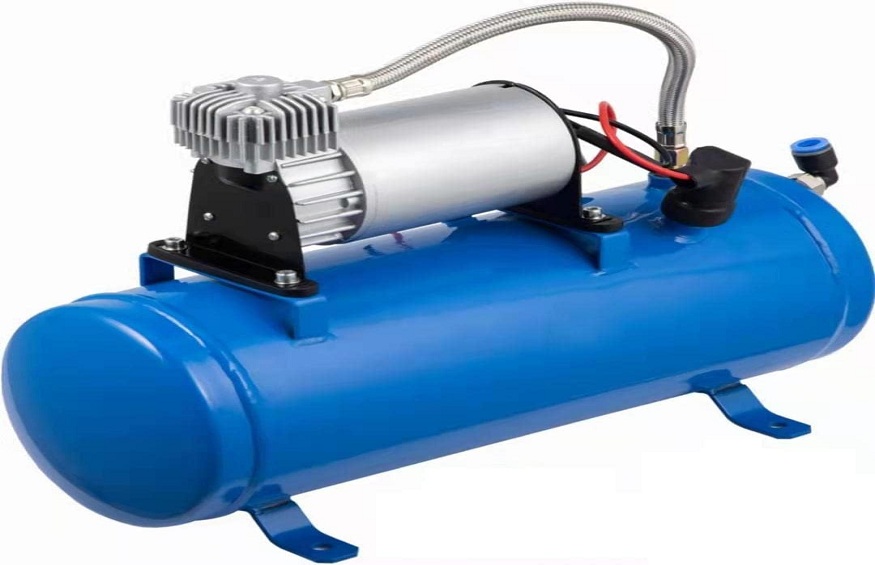
When looking for the right air compressor for shop, the choice between oil-free and oil-lubricated models can be quite daunting. Each type has its own set of advantages and disadvantages, and making the wrong decision can have a significant impact on your operations and your budget. In this blog, we’ll dive deep into the world of air compressors and explore the pros and cons of oil-free and oil-lubricated variants so that you can make an informed choice for your shop application.
The Basics: Oil-Free Air Compressors
Oil-free air compressors, as the name suggests, do not require oil in their operation. These compressors use innovative technologies, such as Teflon-coated components or self-lubricating materials, to ensure smooth functioning without needing oil. The absence of oil means less maintenance and no risk of oil contamination in the compressed air.
Pros of Oil-Free Air Compressors:
- Low Maintenance: One of the most significant advantages of oil-free compressors is their low maintenance requirement. Without oil to change or filters to replace, you can save time and money on upkeep.
- Clean Compressed Air: Since no oil is involved in the compression process, the air produced is exceptionally clean and suitable for applications that demand contaminant-free air, like painting or medical processes.
- Compact and Portable: Oil-free compressors are generally more compact and lightweight than their oil-lubricated counterparts, making them easy to move around the shop as needed.
- Quieter Operation: These compressors operate at lower noise levels, creating a more peaceful working environment for your shop.
Cons of Oil-Free Air Compressors:
- Limited Lifespan: The absence of oil in the compression chamber can lead to more wear on the components, resulting in a shorter overall lifespan than oil-lubricated compressors.
- Less Suitable for Heavy-Duty Applications: Oil-free compressors may struggle to keep up with demanding, continuous-use applications, as they are better suited for light to medium-duty tasks.
Understanding the Basics: Oil-Lubricated Air Compressors
Oil-lubricated air compressors, on the other hand, rely on oil for lubrication and cooling during the compression process. This traditional design has been widely used for decades and is known for its reliability and robust performance.
Pros of Oil-Lubricated Air Compressors:
- Enhanced Durability: The presence of oil in the compression chamber reduces friction and wear, resulting in a more durable and long-lasting compressor.
- Suitable for Heavy-Duty Applications: Oil-lubricated compressors excel in heavy-duty applications that require continuous, high-output air supply, such as industrial manufacturing and automotive repair.
- Efficient Cooling: The oil lubrication system aids in better heat dissipation, preventing the compressor from overheating during prolonged use.
Cons of Oil-Lubricated Air Compressors:
- Regular Maintenance Required: Oil-lubricated compressors demand frequent maintenance, including oil changes and filter replacements, to ensure optimal performance.
- Oil Contamination Risk: Although oil-lubricated compressors produce high-quality compressed air, there is a slight risk of oil carryover, which might not be suitable for sensitive applications like medical equipment or food processing.
Now that we have explored the pros and cons of oil-free and oil-lubricated air compressors, let’s consider some factors to consider when choosing the right one for your shop application.
Factors to Consider When Choosing the Right Air Compressor:
- Usage and Application: Assess your shop’s specific needs and the type of tools or equipment that the compressor will power. Determine whether you require a compressor for light, intermittent use, or heavy-duty continuous operation.
- Compressed Air Quality: Consider the level of air purity needed for your shop application. If your work involves delicate processes like painting or electronics, oil-free compressors may be the better choice.
- Noise Level: Evaluate the noise tolerance levels in your shop. If a quieter environment is essential for your employees’ comfort and productivity, oil-free compressors might be preferable.
- Maintenance Cost and Effort: Factor in each compressor type’s long-term maintenance costs and effort. While oil-free compressors have lower maintenance needs, they might need more frequent replacement due to their shorter lifespan.
- Budget: Finally, weigh the upfront cost of each compressor against its long-term benefits and choose the one that aligns with your budget.
Conclusion
Oil-free and oil-lubricated air compressors have merits and limitations. The choice between the two depends on your shop’s specific needs, including the application, compressed air quality requirements, noise levels, maintenance considerations, and budget constraints.
Choosing the right air compressor is crucial for your shop’s smooth and efficient operation. So take your time, assess your needs carefully, and make an informed choice.
For high-quality air compressors online and expert advice, visit Complete Engineering Solutions. Trust us to provide the perfect solution for your shop’s productivity and growth.
Remember, the right air compressor is the heart of your shop, and it’s an investment that will pay off in the long run. Happy compressing!